The versatility and strength of stainless steel wire have an incredibly broad application area in industry and commerce. Made from the highest-quality alloys, a combination of iron with chromium and nickel, in some cases, it may also include molybdenum and manganese. Its most important characteristic is resistance to corrosion, because of which this material turns out to be effective even in difficult environmental conditions. Its strength and flexibility have made it highly sought after in various industries, including construction, automotive, aerospace, and medical.
There are different sizes, grades, and finishes of stainless steel wire, hence it can be adapted to various applications. Fine wires would be excellent for electrical components and the making of jewellery. In contrast, thicker wires are better used for fencing, welding, and reinforcements of structures. These wires are quite light in weight, and their smooth finish and aesthetic appeal make them quite popular for decorative and architectural projects.
This is why it has high tensile strength and resistance to wear; hence, it can deal with demanding conditions while being able to deliver reliable performance. Its low maintenance and long service life make stainless steel wire efficient and cost-effective for modern industry, ensuring durability and functionality.
What is Stainless Steel Wire?
Stainless steel wire is a thin approximately 0.5 mm to 6 mm diameter (for general purpose) cylindrical metal strand made from different grades of stainless steel. It is flexible and durable even in corrosive environments. These wires are used for industrial, commercial, and household applications.
Manufacturing Process of Stainless Steel Wire
All the stages of making stainless steel wire are explained in detail below.
Raw Material Selection
Melting & Casting
Hot Rolling
Wire Drawing
Annealing (Heat Treatment)
Pickling (Surface Cleaning)
Cold Drawing (Optional)
Surface Finishing
Coiling & Packaging
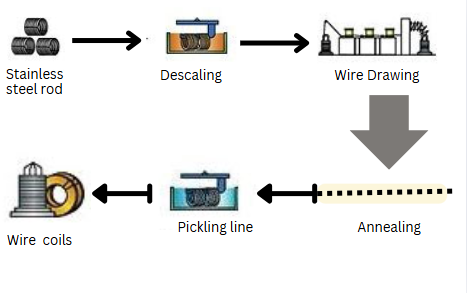
Raw Material Selection:
Stainless steel production begins with using the finest raw material. Stainless alloys of iron, chromium, nickel, molybdenum, and manganese are included in stainless steel production. Depending upon commercial and industrial usages, especially certain grades, are used in industries. Nickel and molybdenum strengthen stainless and make it resistant to corrosion is chromium. The composition to be used is of much importance since it has a direct influence on the properties of the wires at the final stage, such as strength, flexibility, and resistance to corrosion. In addition, the process ensures uniform quality of raw materials without impurities in the production process.
Melting & Casting:
The raw materials are melted in the furnace where alloying takes place. This molten stainless steel guarantees that the metal attains uniform composition and desired mechanical properties. This molten metal is then poured into molds and cast in the form of billets, blooms, or slabs. These billets are used as the base material for further processing. The proper melting and casting ensures that the base material will have no defects and be of high quality, impacting the performance and durability of the final stainless steel wires.
Hot Rolling:
Hot rolling is then applied to the billets or slabs to size and form them. The rolling is carried out at high temperatures that cross the recrystallization temperature of the metal to refine the grain structure and get rid of internal stresses. Hot rolling is the process of converting billets into wire rods with the needed thickness and length for further processing. It makes the wire strong and ductile, in addition to rendering the required uniformity, indispensable in their industrial or commercial utilization.
Wire Drawing:
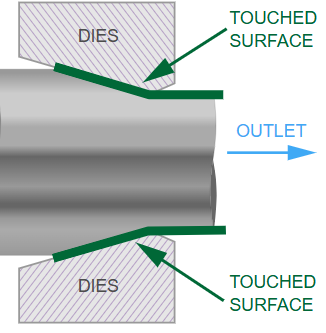
Hot rolled wire rods are fed into wire drawing machines, where the diameter of these wires is reduced to the required thickness. This process leads to wires that are accurate and consistent, which could be adapted to fit various applications. In the course of wire drawing, the rods are drawn at a high tension, hence their surface finish improves, as well as dimensional accuracy. The process strengthens the wires, hence more reliable.
Annealing (Heat Treatment):
The annealing process heats the wires to a strictly controlled temperature, which they then cool slowly. During the process, the wires will regain their ductility and malleability and relieve internal stresses. The improvement in machinability by annealing enables the wires to be further processed and used for applications with minimal defects and flaws. Annealing ensures high-quality and long-term stainless steel wires.
Pickling (Surface Cleaning):
It’s a surface treatment process that will remove the oxides, scales, and other impurities sticking to the surface of the wire. In pickling, it is immersed into acid baths or chemical solutions designed to enhance its surface finish with good corrosion protection. The finished appearance of clean and smooth on pickled wires makes them crucial to applications in industry and decoration.
Cold Drawing (Optional):
Cold drawing is a further process used for obtaining precise dimensions and improved surface finish. Wires in the process are drawn down to a temperature of a normal room to enhance their strength and improve their surface quality. Cold drawing finds its applications best in high precision, such as medical devices and fine electrical components.
Surface Finishing:
In the surface finishing process the wires are polished or coated to enhance their final look and performance. Coatings improve the corrosion resistance and wear resistance of the wires. Polishing gives the wires a smooth and shiny appearance for decorative and aesthetic applications.
Coiling & Packaging:
Final stainless steel wires are wound through coiling machines into uniform coils. These coils are supplied to the industries in the ready-to-use form after proper packaging. Such packaging protects them from damage in handling and transporting and keeps them intact in terms of quality.
Types of Stainless Steel Wire & their Applications
Soft Annealed Stainless Steel Wire:
It is soft annealed stainless steel wire. These are ductile and flexible wires manufactured through the annealing process. It possesses high ductility. These kinds of wires are vastly used in applications such as electrical wiring, binding, and packaging. It is used in the construction and agricultural sector for fencing and tying materials. Its surface finish is smooth and non-corrosive, thus very suitable for outdoor applications.
Spring Stainless Steel Wire:
Spring stainless steel wires have high tensile strength and outstanding elasticity. It becomes widely used in a lot of fields, such as springs, fasteners, suspension systems, in which both flexibility and durability are required. Known for good fatigue resistance and performances that last for a long period, the wires are in demand in aerospace and automotive industries as well as among industrial machinery sectors. Its ability to perform reliably under extreme stress makes it ideal in critical applications under demanding environments.ire. It also provides a balance of strength and flexibility. Generally this wire is available from 0.7 mm to 30 mm diameter
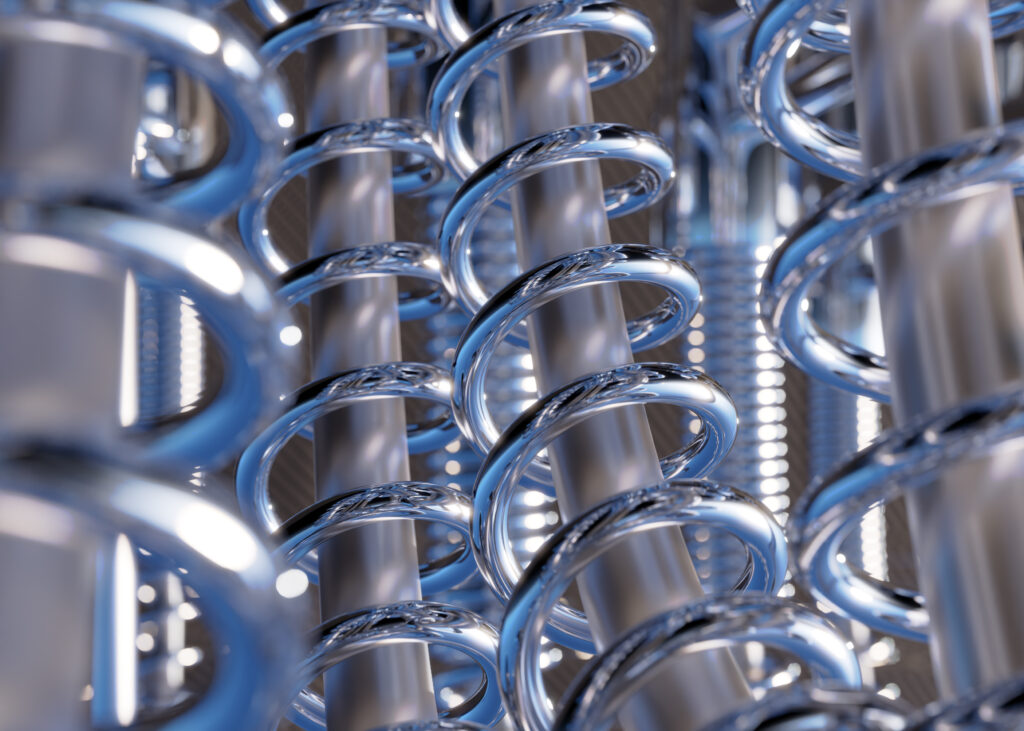
Welding Stainless Steel Wire:
Welding stainless steel wire is one of the specialty types used in welding applications. They are used in critical joints and seams where corrosion resistance as well as strength are required. They use them in oil & gas pipelines, chemical plants as well as shipbuilding wherever precision and high-quality welds are to be made.
Knitted Stainless Steel Wire:
Knitted stainless steel wire is a kind of special material that is commonly used in mesh and filter production. It applies in a great number of areas, such as air filtration systems, mist eliminators, and shielding components. Due to its flexibility and adaptability, this mesh may be tailored for many industrial and environmental purposes, hence turning into one of the most dependable and flexible critical mechanical parts require. Its uses are wide in the automotive and construction industries.
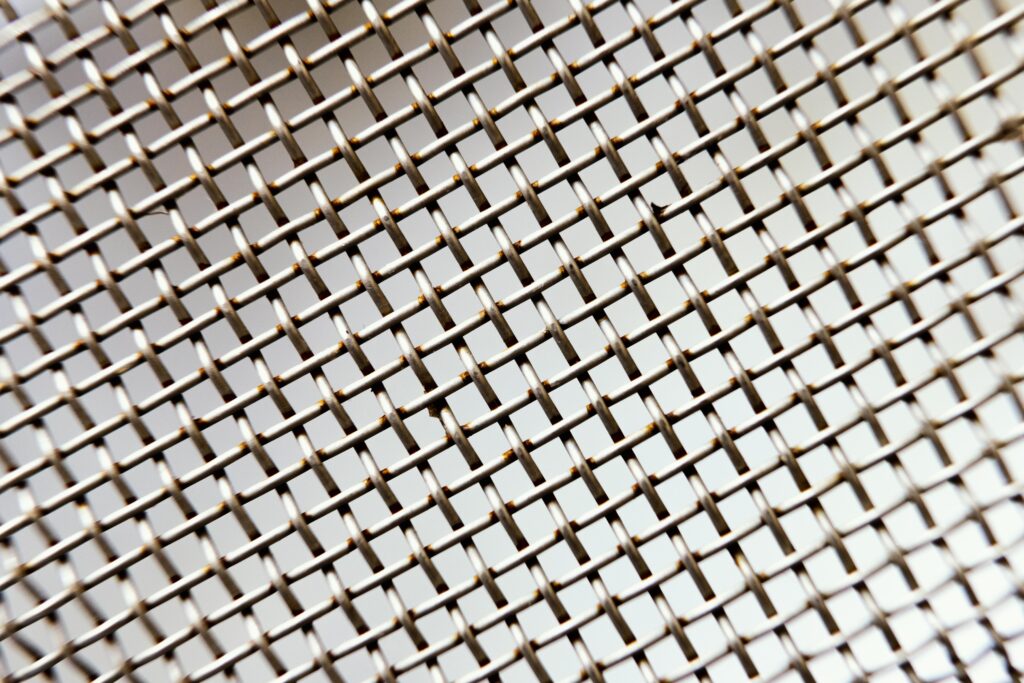
Cold-Heading Stainless Steel Wire:
Cold-heading stainless steel wire is used in the production of high-strength fasteners, bolts, and screws. The wire has very good formability and wear resistance, so it is useful in critical mechanical components. It has wide usage in the automobile and construction industries.
Popular Grades of Stainless Steel Wire and Their Applications
Grade | Applications |
304 | Household items, automotive, food equipment. |
316 | Marine, medical, chemical industries. |
410 | Springs, industrial tools, fasteners. |
430 | Decorative purposes, lightweight applications. |
201 | Cost-effective fencing and retail displays. |
Advantages of Stainless Steel Wire
Corrosion Resistance: The most vital advantage associated with stainless steel wire is its attribute of being corrosion resistant. The combination of chromium and nickel makes this wire rust-proof, even in hostile situations like moisture, humidity, and chemical exposure. This property makes it a better alternative for all marine applications and chemical process industries.
High Strength and Durability: The high tensile strength and toughness of the stainless steel wire make it appropriate for heavy-duty applications. These wires can take up a lot of stress and wear and tear and, therefore, become very reliable in construction, automotive, and aerospace industries.
Versatility: These stainless steel wires are of different grades and sizes, which make them useful in several applications, such as fencing, welding, jewelry making, and manufacturing medical equipment. It is also very much easy to customize and fabricate because of its good machinability and weldability.
Limitations of Stainless Steel Wire
High Upfront Cost: The stainless steel wire is quite pricey compared to mild steel or any other alternatives. This might prove to be a serious limitation for small industries and low-budget projects.
Specialized Equipment and Expertise: Making and welding stainless steel wire requires high-end tools and trained labor. The added processing complexity in this way raises production costs.
Weight and Handling: The high density makes handling and transportation of thick stainless steel wires difficult. More equipment will be needed in large projects, thus raising the cost of a project.
Conclusion
Stainless steel wire is a versatile, corrosion-resistant material with high tensile strength and durability, which enables it to be used in many industrial, commercial, and even domestic sectors. They come in different grades, each with its particular properties that can be adapted to suit the requirements of an industry. Stainless steel wire is mostly used in construction, automotive, medical, and marine industries for the manufacture and maintenance of parts crucial for their activities.
Moreover, its smooth surface and aesthetic appeal make the stainless steel wire all the more suitable for decorative and architectural purposes. Its low-maintenance nature and long life span establish it as a cost-effective and eco-friendly solution. However, high upfront costs and fabrication challenges impose certain limitations, but these can be overcome by proper grade selection and advanced techniques.
Every conceivable aspect has been looked upon and Wire Stainless Steel in modern industries is an integral element in infrastructure developments because it is flexible and has its unique features. It belongs to the branch of secure and efficient measures that guarantee lifelong reliability and performances.
For more detailed knowledge about steel products visit WiserBolt.com!😊
Pingback: TYPES OF HEAT TREATMENTS: A QUICK OVERVIEW - WISERBOLT