Introduction to Cold Rolled Steel
Cold rolled steel refers to a type of steel that has undergone several procedures to improve surface quality, consistent dimensions, and strength. While hot rolled steel is made at high temperatures, cold rolled steel is manufactured at room temperature. Those mentioned characteristics confer on cold rolled steel very unique features: dimensional accuracy and toughness. The above-mentioned properties thus make it a very good choice in the world of industrial uses. It is normally applied in such applications where there are smooth surface finishing requirements of tight tolerances and good mechanical properties.
What is Cold Rolled Steel?
To get cold rolled steel, one has to start with hot rolled steel, which is then rolled at room temperature. This is accomplished in a few steps.
Starting with Hot Rolled Steel: First, hot rolled steel is taken, which has been processed above the recrystallization temperature of 926°C to 1200°C.
Cold Reduction Process: The steel is passed through a cold reduction mill at room temperature in order to decrease the thickness and increase the strength. This also enhances the surface finish and dimensions of the steel.
Annealing and Tempering: Annealing removes the stress from the steel. Hardness can be increased by tempering, which is also called fully hard cold rolled steel and depends upon the final application.
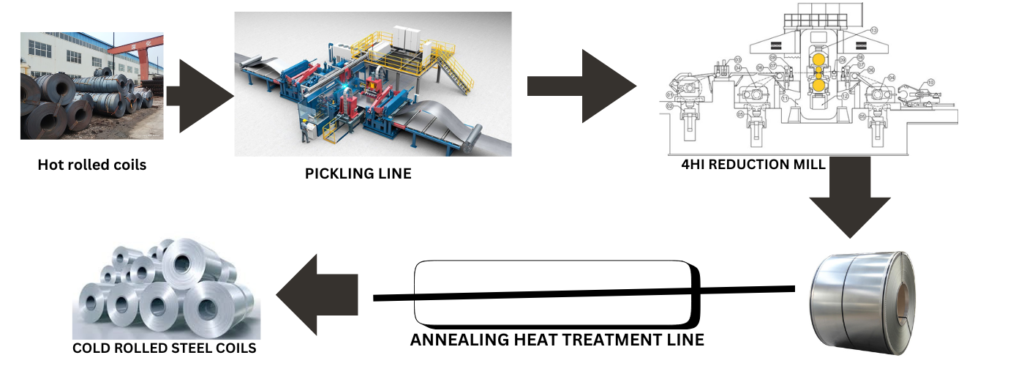
Key Properties of Cold Rolled Steel
Cold rolled steel comes with several benefits, including:
Smooth Surface Finish: Cold rolling gives the steel a smooth and polished surface, ideal for decorative applications or painting, among other forms of further processing.
High Dimensional Accuracy: CR steel thickness and tolerances are very precise, ideal for precision-required parts.
Strength and Hardness: The rolling process increases the strength and hardness of the steel for application in structural and mechanical purposes.
Weldability and Formability: It consists of some grades of cold-rolled steel suitable for easy welding and forming.
Why Do We Manufacture Cold Rolled Steel?
Cold rolled steel is produced to full-fill the demands of many applications. Let us explore what are the main reasons for manufacturing this steel.
a. Precision and Quality
High precision and quality are a few main reasons for the manufacturing of CR steel. Cold rolling gives tight dimension tolerance and high-quality surface, which is indispensable in most industrial applications. Many businesses, especially those within automotive, appliances, and electronics, depend greatly on the exact dimensions found with cold-rolled steel.
b. Enhanced Mechanical Properties
This process increases the strength, durability, and hardness of the steel. CR steel has higher toughness, which is very important in applications like structural and load-supporting parts, such as steel beams and machinery parts.
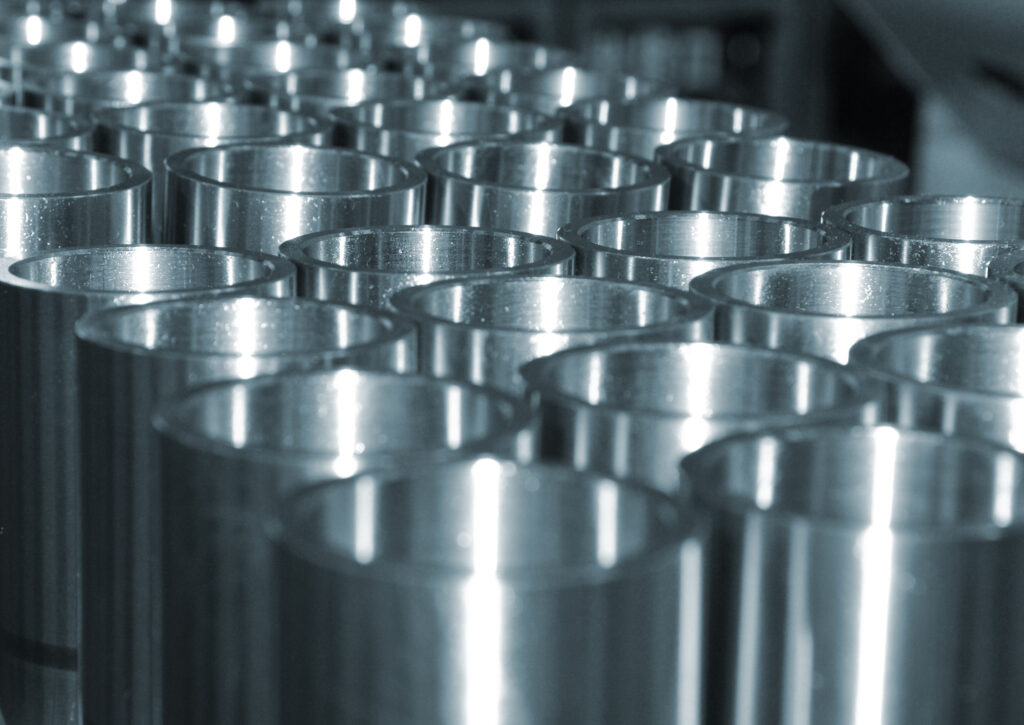
c. Versatility in Applications
The versatility of cold rolled steel makes it useful in many sectors, such as:
- Automotive: CR steel is normally used in the frames of vehicles, body panels, and other components that require a combination of strength and smooth finishes.
- Appliances: Over recent decades, cold rolled steel has increasingly been used in washing machines, refrigerators, ovens, and countless other appliances for its strength and good finish retention.
- Furniture: Office furniture, shelving, cabinets, industrial storage, and in general, whenever strength and appearance are required, cold rolled steel comes into play.
- Construction: CR steel is also used in construction for applications that require accurate dimension and strength, like steel studs, beams, and base steel to manufacture pre-painted galvanized steel and framing systems.
d. Cost Efficiency
Cold rolling adds some expense to the hot rolled steel; however it is cost-effective in the long run as its high precision and surface finish limit further processing.
e. Aesthetic Appeal
The smooth and polished surface of CR steel makes it ideal for products and structures where appearance is important, such as decorative panels, signage, and furniture.
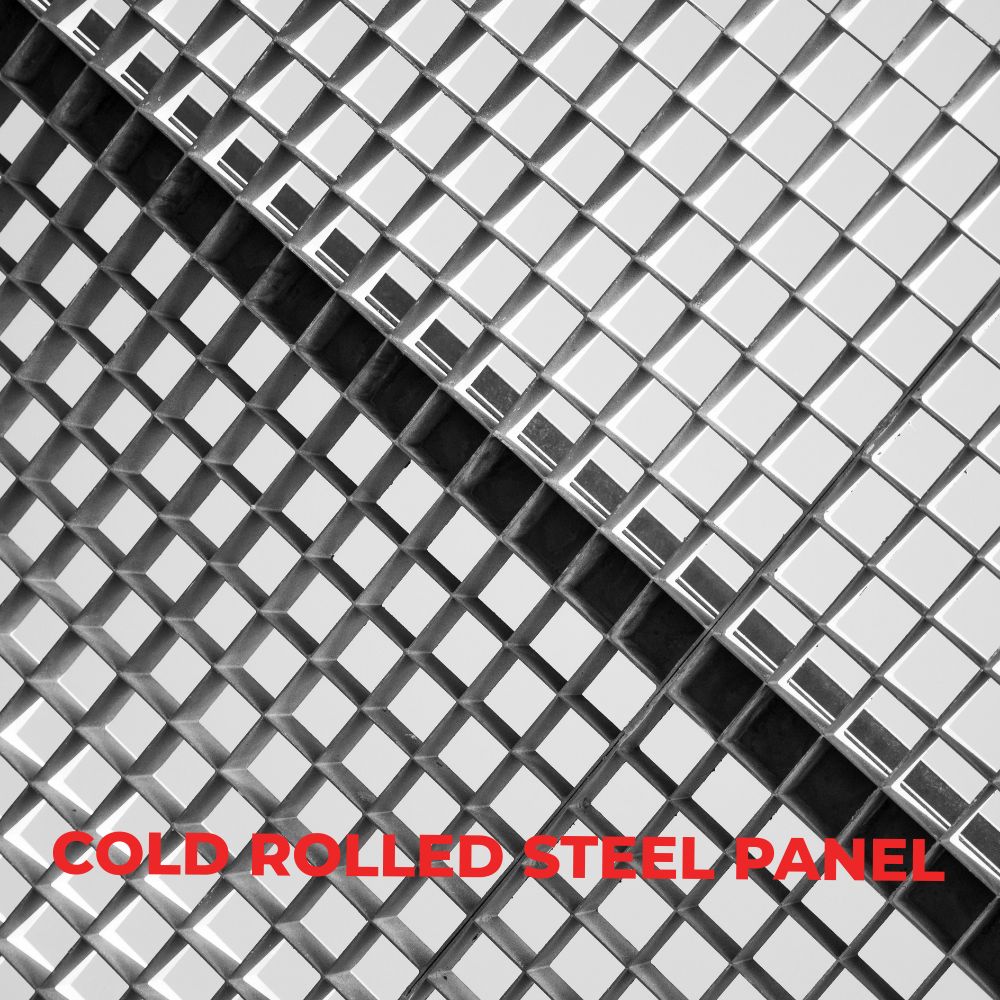
Manufacturing Process of Cold Rolled Steel
Cold rolling is a multistage process by which hot rolled steel becomes CR steel.
Step 1: Pickling
Pickling of the surface of the HR steel takes place before the cold rolling starts. It cleans the oxide layer off the steel surface. Acid solution is used in this process, and it is ready for further processing.
Step 2: Cold Reduction
After pickling, HR steel is passing through a cold reduction mill. Here, the steel is compressed and rolled to the desired thickness. This process takes place at room temperature. This will increase the strength and hardness and also refine the thickness.
Step 3: Annealing (Optional)
It can also be annealed, depending on the end requirements, to relieve internal stresses developed in the processing of CR steel. Annealing is the heating of the steel to some predetermined temperature followed by slow cooling to improve ductility to enhance the ease of working.
Step 4: Temper Rolling
In some instances, cold rolled steel is further temper rolled to improve its surface finish and enhance its mechanical properties. The process of temper rolling can also impart a specific surface texture, which is desirable in end applications.
Step 5: Finishing
Finally, the steel is inspected and cut or coiled to the required dimensions. The steel may also be coated or painted to improve its appearance and resistance to corrosion.
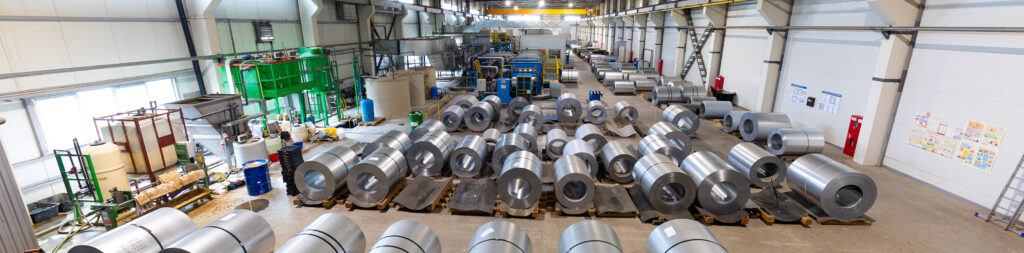
Advantages of Cold Rolled Steel Over Hot Rolled Steel
CSome of the benefits cold rolled steel has over hot rolled steel include:
- Strength: The process of cold rolling work-hardens the steel, increasing its strength.
- Surface Quality: CR steel has a smoother surface finish, which is very suitable for applications requiring aesthetic appeal.
- Tighter Tolerances: CR steel is rolled to exact dimensions with minimal deviation.
- Improved Formability: A few grades of CR steel show better formability and are suitable for bending and shaping processes.
These features make CR steel best suited where strength, precision, and aesthetics are required in applications.
Limitations of Cold Rolled Steel
Cold rolled steel also has some limitations:
Higher Cost: The additional processes involved in cold rolling add to the production cost.
Lower Ductility: CR steel can be brittle in some applications where high ductility is required.
Not Suitable for Large Structural Components: Due to cost and processing constraints, cold rolled steel is not used for large structural applications like I-beams or heavy machinery.
Future of Cold Rolled Steel Manufacturing
With increasing demand in the automotive, construction, and appliance sectors, the future of CR steel manufacturing is bright. Technological advancement makes possible the production of high-strength, eco-friendly steel that will be able to meet the needs of the future. With energy-efficient processes and sustainable practices, the future of CR steel manufacturing is very promising.
Conclusion
Cold rolled steel is manufactured to completely meet the needs of such industries as strength, precision, and smooth surface finish. It has unique properties that make it an integral part in industries such as automotive, construction, and appliances due to its wide range of applications. With the passage of time, new technology will make manufacturing cold rolled steel more efficient and environmentally friendly, further increasing its demand.
Pingback: HOT ROLLED STEEL - Importance in Our Life
Pingback: HOT ROLLED CARBON STEEL PIPES - STEEL PRODUCT INFO.